Solutions for Carbon Fibers
Auto racing can no longer do without the miracle material, carbon: The monocoque alone of a Formula 1 racing car is made from approximately 1500 carbon fiber sheets. Carbon is - stronger than steel, but about five times lighter: That makes for speed and saves fuel. But carbon has also found its way into many other applications we encounter daily: Airplane components, walking sticks, fishing rods, bicycles and many other items are made from this material.
Usually between 1,000 and 20,000 fibers are processed to form the yarn. The statement "Made with SAHM Winding Technology“ comes with our promise that your carbon fibers will be wound with the highest possible precision for a positive impact on the quality of the final material.
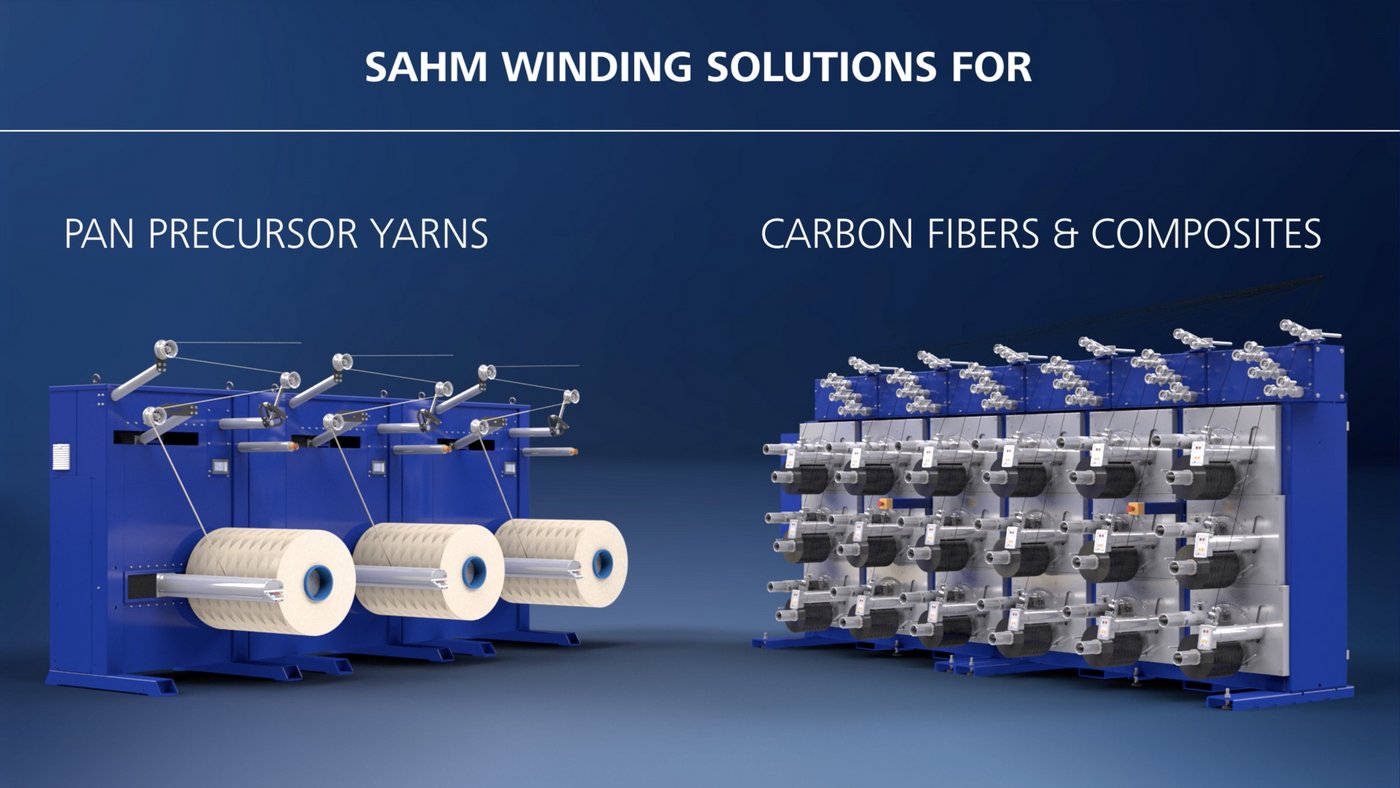
SAHM 872XE
SAHM 830XE & 840XE
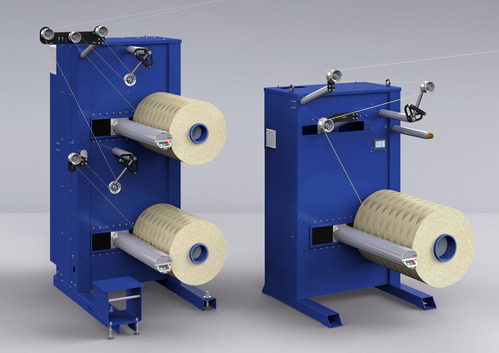
SAHM 830XE & 840XE
The Jumbo Winders offer modular design for heavy-weight PAN bobbins.
SAHM 460XE Series
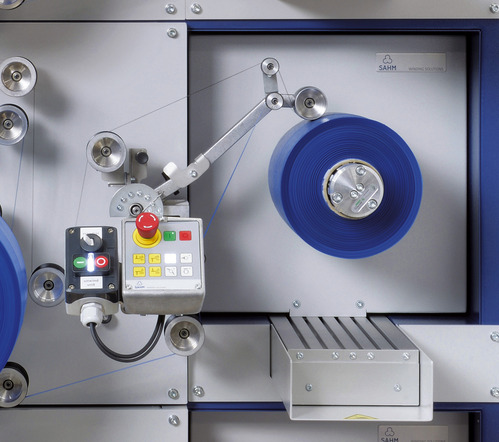
SAHM 460XE Series
These precision parallel winding machines with traversing spindle are specially designed to meet the demanding requirements that come with handling sensitive materials and tapes.
The winders of the SAHM 460XE series produce bobbins of consistently high quality and support a multitude of bobbin types and winding materials. Their low maintenance design ensures reliable and highly predictable machine availability.
SAHM T1 RackWinder
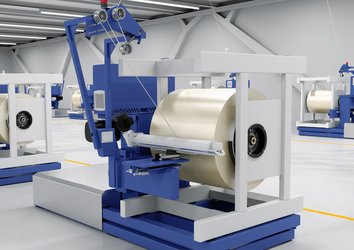
SAHM T1 RackWinder
Combination of all maximum values is not possible
- Applications
- Wet spinning and air-gap spinning
- PAN Precursor yarns
- Advantages
- Fast changeovers
- Easy shipping of T1 MultiRacks
- Quality Control Management with NFC tags
- Flexible winding concept
- Technical dataWinding technologyPrecision cross windingDriveFrequency inverter-controlledFrame1-tierTiter12 to 60 K (others on request)Winding speedUp to 150 m/min for wet spinning, up to 600 m/min for air-gap spinning (others on request), 0 to 20 m/min for unwindingWinding ratioElectronicTraverse lengthMax. 900 mmPackage diameterMax. 1,500 mmStart diameter600 mmPackage weightMax. 1.2 ton (depends on density)Rack dimensionsH x L x W: 1,700 mm x 1,700 mm x 1,150 mm*others on request.
Combination of all maximum values is not possible - Features
- Electronically controlled winding ratio
- Central process control unit for input, display and storage of process and machine parameters
- A/C motor-driven and tension-controlled winding and unwinding on creel side
- Easy thread up function with catch and cut function
- Pneumatic doffing system for T1 MultiRack during changeover
- Options
- Special traverse system for two selectable traverse widths for rack winding and for tube winding (between 900 mm and 750 mm)
- Automatic robot system for handling racks on winding, storage and on creel side
- Wet spinning and air-gap spinning
- PAN Precursor yarns
SAHM 880XE
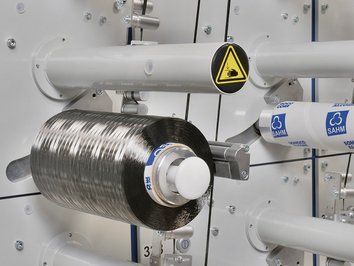
SAHM 880XE
Combination of all maximum values is not possible
- Applications
- Carbon fibers
- Specific towpregs
- Advantages
- Excellent package quality
- Quick and efficient product changes
- Electronic input of all winding parameters
- Compact and modular design
- Reproducible yarn package formation
- Technical dataTiter1 to 60 K*Winding speed1 to 15 m/minTraverse lengthMax. 250 mmDriveFrequency-controlledFrame4-tierTube inside diameter76.2 mmTube length280/290 mmWinding ratioElectronicYarn tensionElectronically adjustablePackage diameterMax. 250 mmWinding technologyPrecision cross winding*others on request.
Combination of all maximum values is not possible - Features
- Electronically controlled and infinitely variable winding ratio
- Central Process Control Unit (HMI 12" touch screen) for input, display and storage of process and machine parameters
- Possible speed synchronization with the preceeding process
- Doffing timer function
- Advanced tension control with strain gauge system (yarn guide roller with implemented tension sensor)
- Options
- Pneumatic mandrel
- Variable traverse lengths
- HMI 15" touch screen with high capacity processor for SQL database
- Label printing system
- Carbon fibers
- Specific towpregs
CarbonStar II - standard
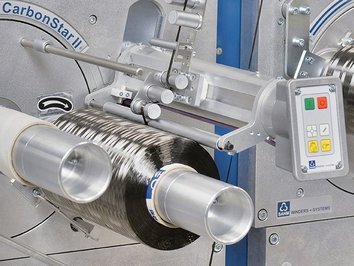
CarbonStar II - standard
Combination of all maximum values is not possible
- Applications
- Carbon Fibers
- Specific Towpregs
- Advantages
- Quick and efficient product changes
- Zero production waste - no downtime during bobbin changeover
- Metered yarn length
- Bobbin changeover reliability of 99.8 %
- Highest operating safety - yarn is caught and cut at rear of bobbin
- Minimum yarn tail after automatic changeover
- Technical dataTiter3 to 60 K*Winding speed2 to 15 m/minTraverse lengthMax. 250 mmFrame3-tierTube inside diameter76.2 mmTube length280 mmWinding ratioElectronicPackage weightUp to 12 kgYarn tensionElectronically adjustablePackage diameterMax. 250 mmWinding technologyPrecision cross windingBobbin mandrelPneumaticalParking position with push off deviceNot included (option available)*others on request.
Combination of all maximum values is not possible - Features
- Automatic bobbin changeover on reaching one of the following criteria: yarn length, winding time, package weight, package diameter or external signal
- Quick and efficient product changes by electronic data input of all winding parameters
- Electronically controlled winding ratio
- Central process control unit (HMI touch screen) for input, display and storage of process and machine parameters
- Tube inside diameter (76.2 mm) tolerance + 0.5 mm possible
- Options
- Variable traverse lengths
- HMI touch screen with high capacity processor for SQL database
- Interface to DCS
- Adaptable to an automatic bobbin handling system
- Frame unit with 6 heads
- Label printing system
- Carbon Fibers
- Specific Towpregs
CarbonStar II - big
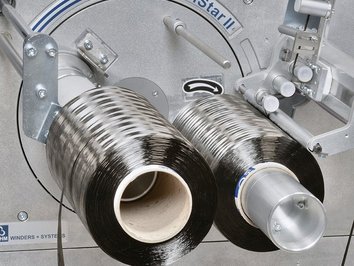
CarbonStar II - big
Combination of all maximum values is not possible
- Applications
- Carbon Fibers
- Specific Towpregs
- Advantages
- Quick and efficient product changes
- Zero production waste - no downtime during bobbin changeover
- Metered yarn length
- Bobbin changeover reliability of 99.8 %
- Highest operating safety - yarn is caught and cut at rear of bobbin
- Minimum yarn tail after automatic changeover
- Technical dataTiter12 to 60 K*Winding speed2 to 15 m/minTraverse lengthMax. 250 mmFrame3-tierTube inside diameter76.2 mmTube length280 mmWinding ratioElectronicPackage weightUp to 20 kgYarn tensionElectronically adjustablePackage diameterMax. 320 mmWinding technologyPrecision cross windingBobbin mandrelPneumaticalParking position with push off deviceIncluded*others on request.
Combination of all maximum values is not possible - Features
- Automatic bobbin changeover on reaching one of the following criteria: yarn length, winding time, package weight, package diameter or external signal
- Quick and efficient product changes by electronic data input of all winding parameters
- Electronically controlled winding ratio
- Central process control unit (HMI touch screen) for input, display and storage of process and machine parameters
- Tube inside diameter (76.2 mm) tolerance + 0.5 mm possible
- Options
- Variable traverse lengths
- HMI touch screen with high capacity processor for SQL database
- Interface to DCS
- Adaptable to an automatic bobbin handling system
- Frame unit with 6 heads
- Label printing system
- Carbon Fibers
- Specific Towpregs
CarbonStar 2-cop
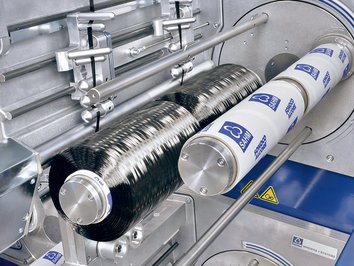
CarbonStar 2-cop
Combination of all maximum values is not possible
- Applications
- Carbon fibers
- Specific towpregs
- Advantages
- Maximum efficiency by production of two bobbins (each up to 20 kg) on one winding head
- Two exact length, high quality spools with our patented diameter control
- Bobbin change-over reliability of 99.8 %
- Highest operating safety due to automatic change-over
- Energy savings from the latest drive technology
- Minimum space requirement
- Very low maintenance costs
- Zero production waste - no downtime during bobbin changeover
- Metered yarn length
- Technical dataTiter3 to 60 K*Winding speed2 to 20 m/minTraverse length2 x 250 mmDriveFrequency-controlledFrame1-, 2- or 3-tierTube inside diameter76.2 mmTube length280 mmWinding ratioElectronicPackage weightUp to 20 kg each bobbinYarn tensionElectronically adjustablePackage diameterMax. 320 mmWinding technologyPrecision cross winding*others on request.
Combination of all maximum values is not possible - Features
- Automatic bobbin changeover on reaching one of the following criteria: yarn length, winding time, package weight, package diameter or external signal
- Quick and efficient product changes by electronic data input of all winding parameters
- Electronically controlled winding ratio
- Central process control unit (HMI 12" touch screen) for input, display and storage of process and machine parameters
- Tube inside diameter (76.2 mm) tolerance + 0.5 mm possible
- Options
- HMI 15" touch screen with high capacity processor for SQL database
- Interface to DCS
- Frame unit with 9 heads
- Label printing system
- Carbon fibers
- Specific towpregs
SAHM 810XE
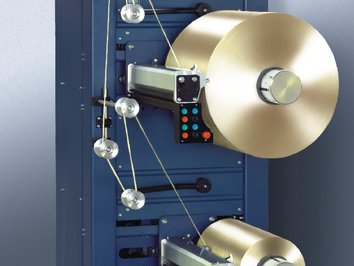
SAHM 810XE
70 to 400 m/min
Combination of all maximum values is not possible
- Applications
- PAN Precursor Fibers
- Advantages
- Excellent package quality and reproducible yarn package formation
- Compact and modular design
- Alarm management (yarn break, yarn length, package diameter)
- Electronic input of all winding parameters
- Pneumatic push-off device
- Technical dataTiter3 to 18 K*Winding speed50 to 150 m/min
70 to 400 m/minTraverse length500 mmDriveFrequency-controlledFrame1- or 2-tierTube inside diameter144 mm*Tube lengthMax. 550 mmWinding ratioElectronicPackage weightMax. 120 kgPackage diameterMax. 600 mm*others on request.
Combination of all maximum values is not possible
- PAN Precursor Fibers
SAHM 832XE
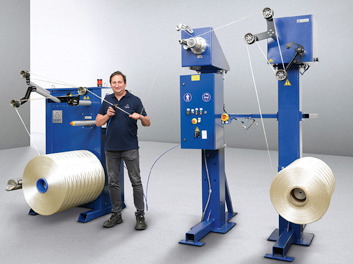
SAHM 832XE
Combination of all maximum values is not possible
- Applications
- PAN precursor yarns
- Advantages
The SAHM 832XE supports standardization of bobbins on the creel side through splicing of short bobbins into a single large standard size. This reduces waste and allows for longer periods of uninterrupted production for higher efficiency and throughput.
- Technical dataTiter3 to 60 K*Winding speed50 to 200 m/minTraverse length700, 750 or 800 mmDriveFrequency-controlledFrame1-tierTube inside diameter133, 140 or 144 mmTube length750, 800 or 850 mmWinding ratioElectronicPackage weightMax. 350 kg (depending on density)Package diameterMax. 800 mmWinding technologyPrecision cross winding*others on request.
Combination of all maximum values is not possible - Features
- Electronically controlled and infinitely variable winding ratio
- Central Process Control Unit for input, display and storage of process and machine parameters
- Speed synchronization between unwinding and rewinding
- Stop and start up function with variable package diameter before and after splicing (alternatively by yarn length or package weight)
- A/C motor driven and tension-controlled unwinding
- Unwinding speed adjustment via potentiometer
- Freely programmable prewarning and target rewinding length
- Automatic speed reduction when prewarning length is reached
- Automatic stop when target length is reached - Godet roll for tension control between unwinding and rewinding
- Pneumatic mandrels for unwinding and rewinding
- Pneumatic doffer for rewinding position
- Options
- Hand-held suction device for doffing procedure
- Hand-held splicing device for splicing of two bobbin ends
- Special traverse system for two selectable traverse widths (either between 500 and 750 or 500 and 800 mm)
- Spindles with ball bearings for easy doffing
- PAN precursor yarns